Industrial pilots
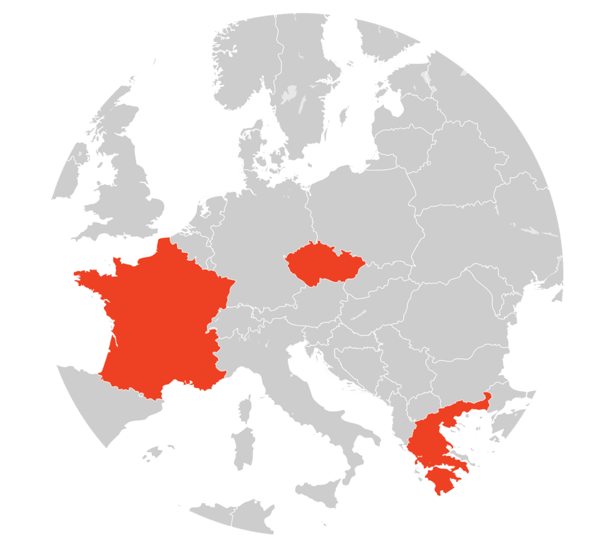
FRANCE
Czechia
GREECE
France

Overall Description

Deburring on reactor pylon
Challenges: (i) the poor accuracy of lightweight or flexible robots, (ii) the need to accurately relocate hole positioning, leading to (iii) adaptation of both the mission (defined by long task sequences) and the movements, (iv) subsequent programming costs, and (v) operators might disturb the process, and their safety must be enforced.
Improvements: (i) safely allow operator in workspace, (ii) no need to stop production during hours of human reprogramming, (iii) instant reset of the mission after security procedure (<10 seconds automatic), and (iv) reduced time to deliver the final product (20%).

Solar Array Assembly
Challenges: (i) the poor accuracy of lightweight or flexible robots, (ii) the required accuracy of the fluid disposal, (iii) the need to relocate and follow the contour of the solar arrays using visual feedback, (iv) operators might disturb the process and their safety must be enforced, (v) sensitive product that can be damaged by the robot.
Improvements: (i) employee exposure to chemical fumes (- 50%), (ii) disposal quality (+10%), (iii) reduced dust production compared to operators (-50%), (iv) task automation with no time loss due to robot safety enforcement, (v) tracking accuracy despite occlusion (<5mm).
Greece

Overall Description
Gluing reinforcement parts in the cabinâs false ceiling


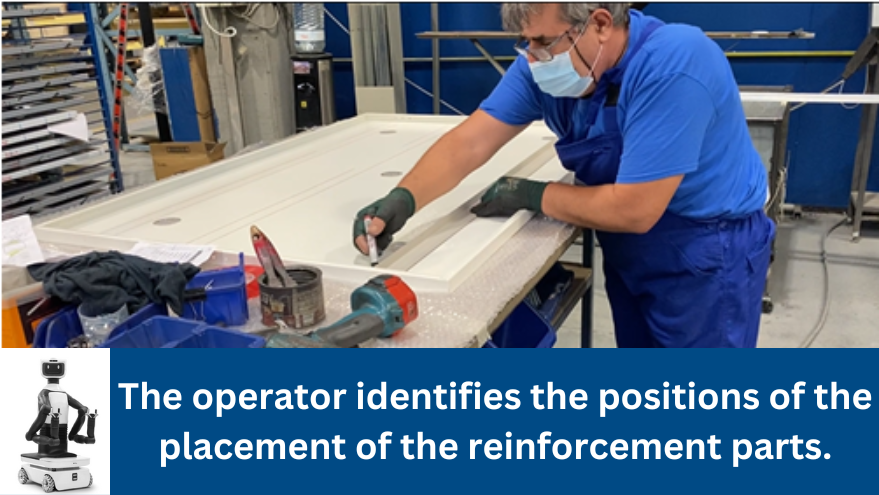
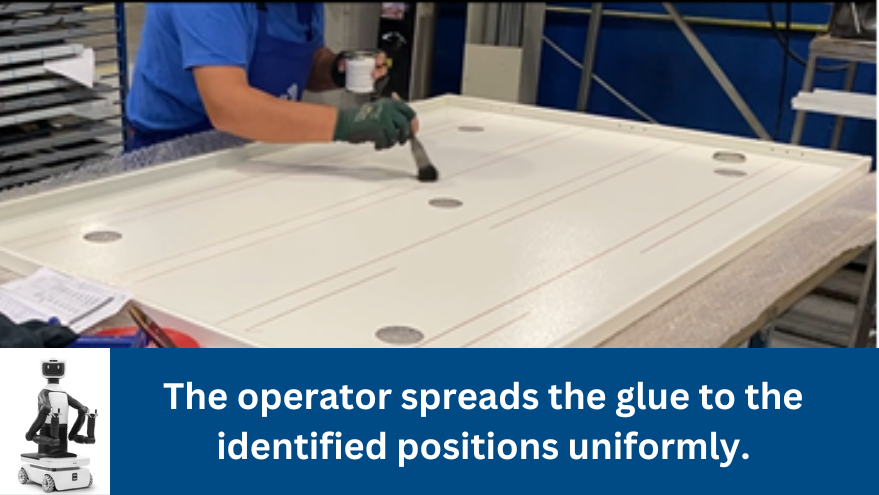


Floor covering material gluing and assembly




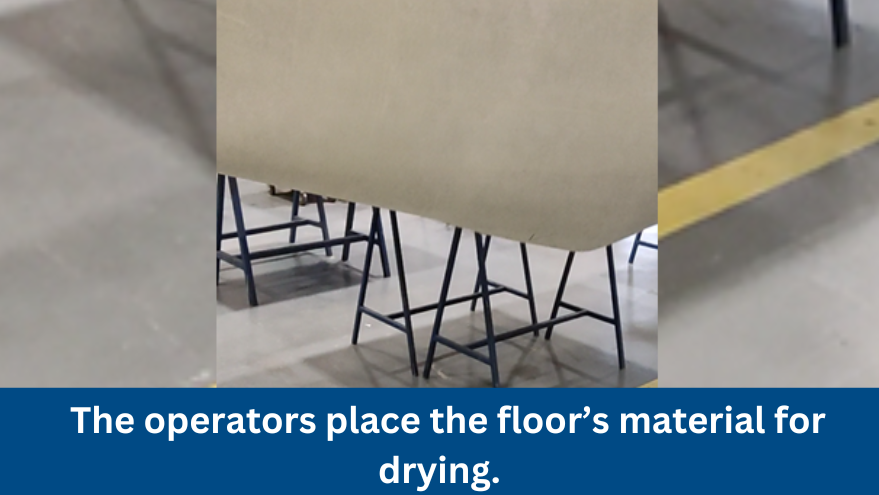

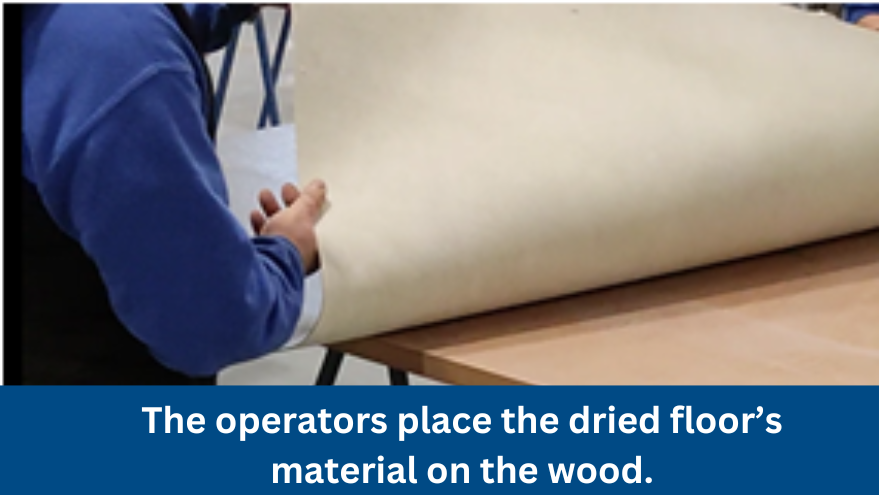
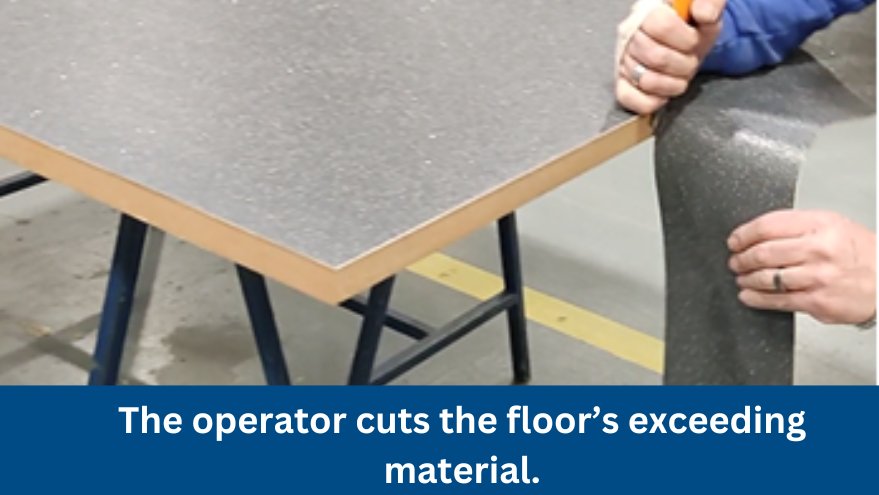
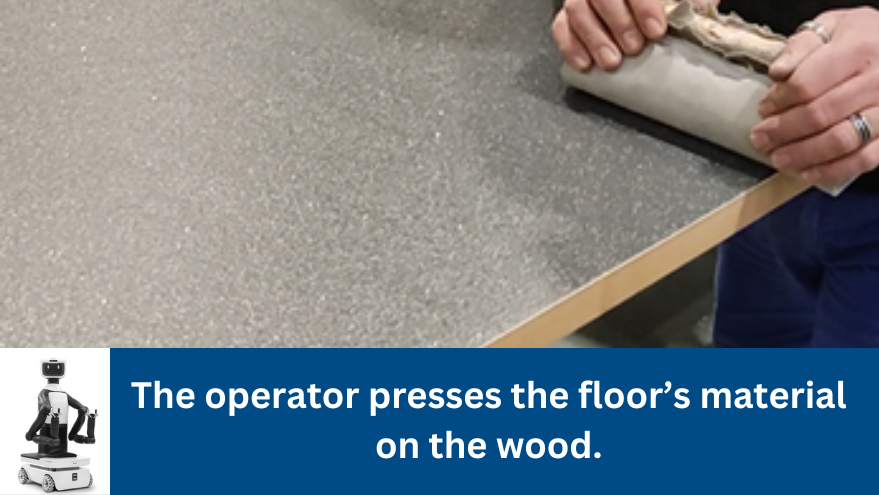
Czechia
Overall Description
The THIMM Packaging Manufacturing industrial pilot will be implemented in THIMMâs facilities in VÅ¡etaty, Czech Republic. The pilot will focus on two case studies: inserting small plastic pieces into the cardboard and removing cardboard waste from the sheet. Our ambition is to automate these procedures as much as possible using the KUKA robots with capabilities similar to TIAGo AGIMUS robots, equipped with AGIMUS software for agile production.
Inserting small plastic pieces into the cardboard






This case study will cover the processes involved in inserting small plastic pieces into prefabricated holes in the cardboard sheets. The KUKA robot will help the operators by localizing the plastic pieces, picking them up, and using combined haptic and vision feedback to insert the pieces accurately into the holes.
ð¯ Given that the operators and the robot will share the same workspace and that the cardboard sheets vary in size and texture, the robot's versatility and accuracy are essential. With the help of the KUKA robot, it is expected that the productivity of this task will increase by 15% compared to human operators.
Removing cardboard waste from the sheet
Description: This case study will cover the processes involved in removing cardboard waste from pre-cut holes in the sheets. The KUKA robot will help the operators by localizing the cardboard sheets and the waste, using a tool to remove the waste, and performing automatic visual quality inspection to ensure all waste has been removed.




ð¯ Given that the operators and the robot will share the same workspace and that the cardboard sheets vary in size and texture, the robot's versatility and accuracy are essential. Task automation with no time loss due to robot safety enforcement is expected for this case study.
France

Overall Description

Deburring on reactor pylon
Challenges: (i) the poor accuracy of lightweight or flexible robots, (ii) the need to accurately relocate hole positioning, leading to (iii) adaptation of both the mission (defined by long task sequences) and the movements, (iv) subsequent programming costs, and (v) operators might disturb the process, and their safety must be enforced.
Improvements: (i) safely allow operator in workspace, (ii) no need to stop production during hours of human reprogramming, (iii) instant reset of the mission after security procedure (<10 seconds automatic), and (iv) reduced time to deliver the final product (20%).

Solar Array Assembly
Challenges: (i) the poor accuracy of lightweight or flexible robots, (ii) the required accuracy of the fluid disposal, (iii) the need to relocate and follow the contour of the solar arrays using visual feedback, (iv) operators might disturb the process and their safety must be enforced, (v) sensitive product that can be damaged by the robot.
Improvements: (i) employee exposure to chemical fumes (- 50%), (ii) disposal quality (+10%), (iii) reduced dust production compared to operators (-50%), (iv) task automation with no time loss due to robot safety enforcement, (v) tracking accuracy despite occlusion (<5mm).
Greece

Overall Description
Gluing reinforcement parts in the cabinâs false ceiling


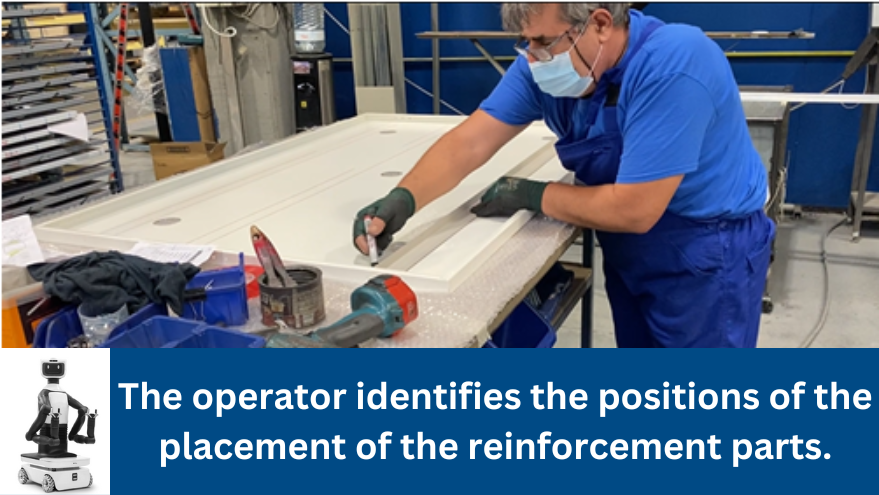
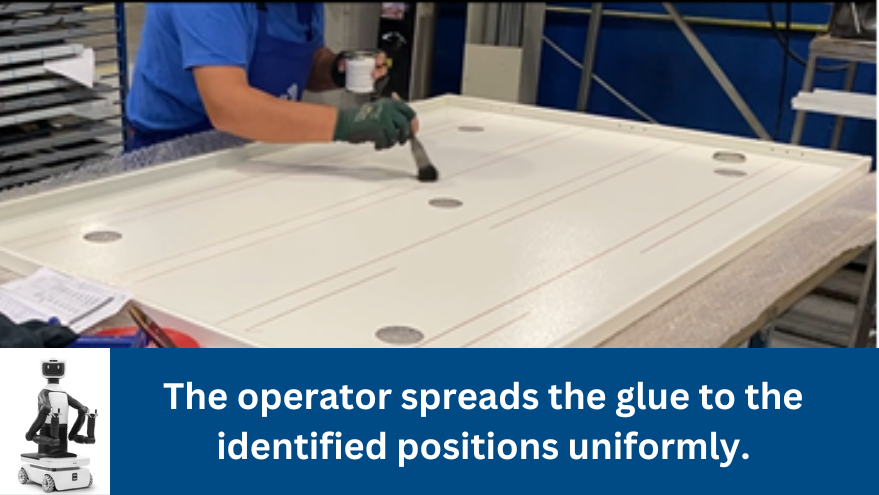


Floor covering material gluing and assembly




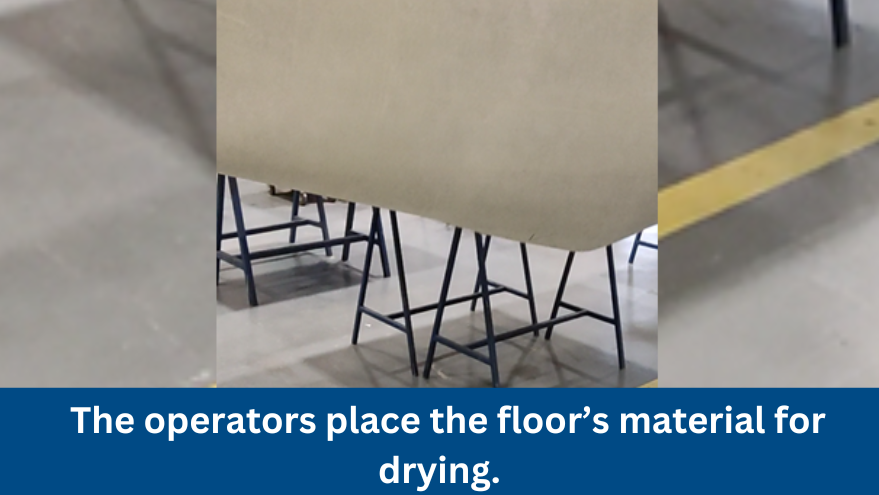

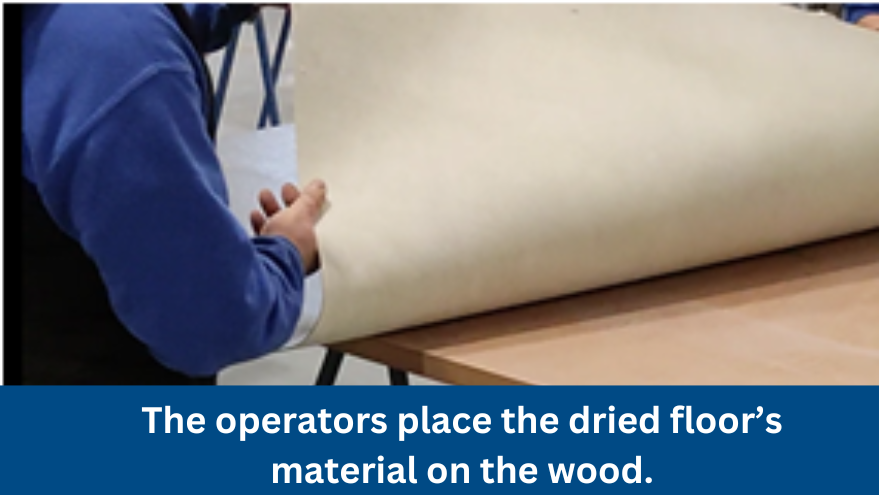
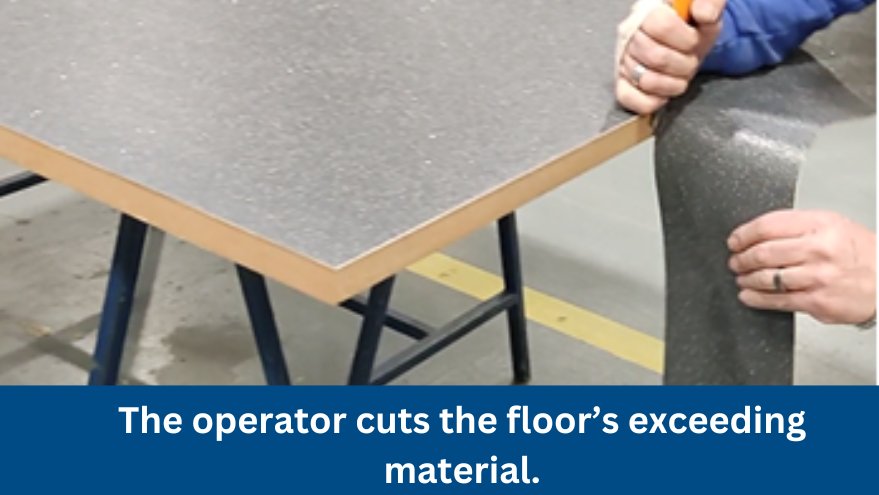
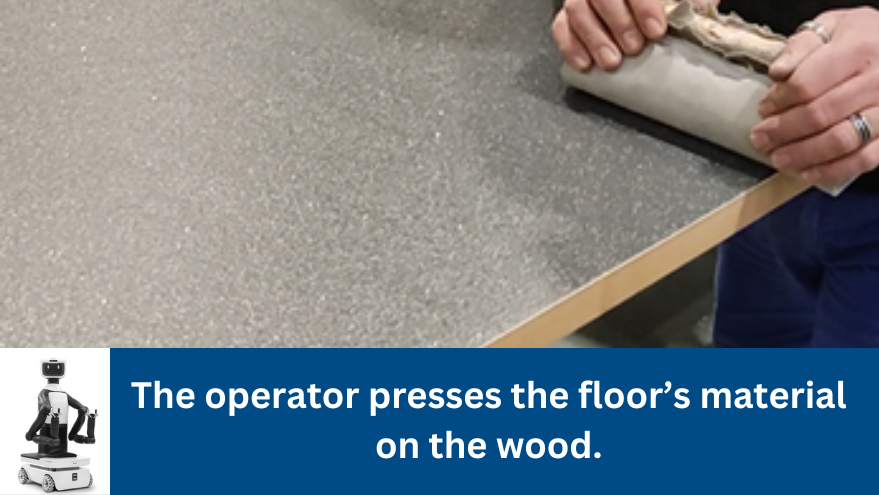
Czechia

Overall Description

Gluing reinforcement parts in the cabinâs false ceiling
Challenges: (i) task accuracy while safely sharing workspace with operators, (ii) the versatility required due to the different shapes of the cardboard displays, (iii) the required accuracy of the glue disposal, and (iv) overall productivity.
Improvements: i) glue disposal quality (+30%), (ii) task automation with no time loss due to robot safety enforcement, (iii) tracking accuracy despite occlusion (<5mm).

Inserting small plastic pieces into the cardboard
Description: This case study will cover the processes involved in inserting small plastic pieces into prefabricated holes in the cardboard sheets. The KUKA robot will help the operators by localizing the plastic pieces, picking them up, and using combined haptic and vision feedback to insert the pieces accurately into the holes.
Challenges: (i) operators might disturb the process, and their safety must be enforced, (ii) sensitive product parts that can be damaged by the robot, (iii) high accuracy in bin picking of small parts, (iv) handling diverse large, light, and flexible cardboards.
Improvements: (i) task automation with no time loss due to robot safety enforcement, (ii) tracking accuracy despite occlusion (<5mm).

Removing cardboard waste from the sheet
Description: This case study will cover the processes involved in inserting small plastic pieces into prefabricated holes in the cardboard sheets. The KUKA robot will help the operators by localizing the plastic pieces, picking them up, and using combined haptic and vision feedback to insert the pieces accurately into the holes.
This case study will cover the processes involved in removing cardboard waste from pre-cut holes in the sheets. The KUKA robot will help the operators by localizing the cardboard sheets and the waste, using a tool to remove the waste, and performing automatic visual quality inspection to ensure all waste has been removed.
ð¯ Given that the operators and the robot will share the same workspace and that the cardboard sheets vary in size and texture, the robot's versatility and accuracy are essential. With the help of the KUKA robot, it is expected that the productivity of this task will increase by 15% compared to human operators.

ð¯ Given that the operators and the robot will share the same workspace and that the cardboard sheets vary in size and texture, the robot's versatility and accuracy are essential. Task automation with no time loss due to robot safety enforcement is expected for this case study.
France

Overall Description

Deburring on reactor pylon
Challenges: (i) the poor accuracy of lightweight or flexible robots, (ii) the need to accurately relocate hole positioning, leading to (iii) adaptation of both the mission (defined by long task sequences) and the movements, (iv) subsequent programming costs, and (v) operators might disturb the process, and their safety must be enforced.
Improvements: (i) safely allow operator in workspace, (ii) no need to stop production during hours of human reprogramming, (iii) instant reset of the mission after security procedure (<10 seconds automatic), and (iv) reduced time to deliver the final product (20%).

Solar Array Assembly
Challenges: (i) the poor accuracy of lightweight or flexible robots, (ii) the required accuracy of the fluid disposal, (iii) the need to relocate and follow the contour of the solar arrays using visual feedback, (iv) operators might disturb the process and their safety must be enforced, (v) sensitive product that can be damaged by the robot.
Improvements: (i) employee exposure to chemical fumes (- 50%), (ii) disposal quality (+10%), (iii) reduced dust production compared to operators (-50%), (iv) task automation with no time loss due to robot safety enforcement, (v) tracking accuracy despite occlusion (<5mm).
Greece

Overall Description

Gluing reinforcement parts in the cabinâs false ceiling
Challenges: task accuracy while safely sharing workspace with operators, ii) the versatility required due to the different shapes of the ceiling components, (iii) the required accuracy of the glue disposal, and (iv) overall productivity (manually repeated tasks require significant time).
Improvements: (i) Employee exposure to chemical fumes (-90%) (ii) glue disposal quality (+30%) and quantity improving (iii) chemical management (-90%), and (v) Increased productivity (+15%).

Floor covering material gluing and assembly
Challenges: (i) task accuracy while safely sharing workspace with operators, (ii) the required accuracy of the glue disposal, (iii) the required accuracy for assembling, and (iv) overall productivity (manually repeated tasks require significant time).
Improvements: (i) Employee exposure to chemical fumes (-90%), (ii) Creation of a production line without gaps and manual handling of materials which results in reduced stress (-20%) and improved quality (+20%), (ii) Increased production rate (+20%)
Czechia

Overall Description

Gluing reinforcement parts in the cabinâs false ceiling
Challenges: (i) task accuracy while safely sharing workspace with operators, (ii) the versatility required due to the different shapes of the cardboard displays, (iii) the required accuracy of the glue disposal, and (iv) overall productivity.
Improvements: i) glue disposal quality (+30%), (ii) task automation with no time loss due to robot safety enforcement, (iii) tracking accuracy despite occlusion (<5mm).

Inserting small plastic pieces into the cardboard
Challenges: (i) operators might disturb the process, and their safety must be enforced, (ii) sensitive product parts that can be damaged by the robot, (iii) high accuracy in bin picking of small parts, (iv) handling diverse large, light, and flexible cardboards.
Improvements: (i) task automation with no time loss due to robot safety enforcement, (ii) tracking accuracy despite occlusion (<5mm).